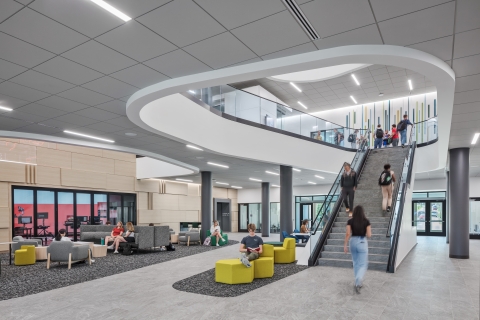
Considerations for Repurposing a Speculative Office Building into Research and Development Laboratories
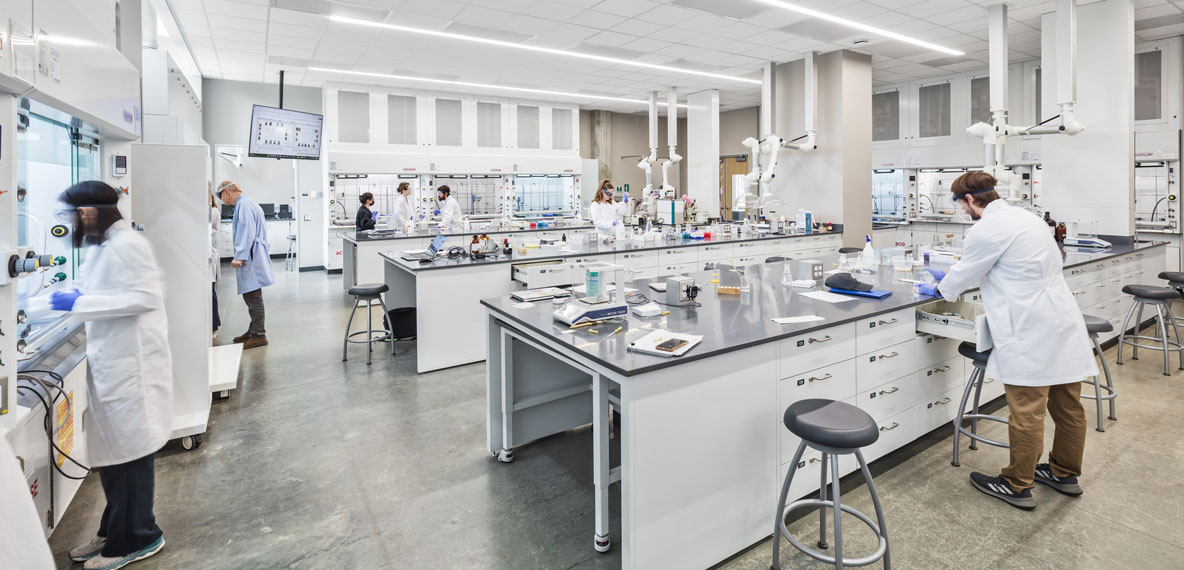
As demand for life sciences and biotech innovation accelerates, companies are facing a critical real estate question: build new or adapt existing space? Increasingly, organizations are opting to repurpose speculative office buildings—originally designed for flexible commercial use—into high-performance research and development (R&D) laboratories.
Transforming speculative office buildings into modern laboratories involves more than just architectural redesign—it requires a delicate balance between innovation and practicality. Clients may initially focus on whether the building has sufficient space and is situated in a favorable location. However, critical factors across architectural, structural, and MEP (mechanical, electrical, and plumbing) systems must be considered.
Repurposing office space into functional lab environments offers speed-to-market advantages and potential cost savings, but only when the building’s core systems can support the specialized demands of scientific research. From floor loads and ventilation to hazardous material handling and biosafety requirements, success hinges on early, integrated planning across disciplines.
Architectural Requirements for Office-to-Lab Conversions
One of the first challenges is adapting the building envelope to meet the strict environmental controls required in lab settings. While offices prioritize comfort, labs demand consistency.
- Thermal performance and energy efficiency: Most office buildings will require insulation upgrades to support temperature stability and reduce energy loss.
- Light management: Windows should be evaluated and potentially retrofitted to control UV exposure, which can affect sensitive experiments, while still providing access to natural light.
- Air and moisture control: Maintaining airtightness is essential for maintaining pressure differentials and preventing contamination.
Freight elevator access is also a core design issue. Laboratories depend on the reliable movement of heavy and sensitive equipment and the secure transport of chemicals and supplies. If a freight elevator exists, its location relative to lab spaces and loading docks must be carefully assessed. If one does not exist, adding one may require structural reinforcement—especially on upper floors—and a dedicated, uninterrupted power supply.
Another key architectural constraint involves the storage and use of hazardous materials. Building codes limit the types and quantities of materials allowed on each floor, often becoming more restrictive the higher up in a structure. This makes early planning essential to avoid costly redesigns.
Finally, zoning and permitting must be reviewed early in the process. Lab use may not be permitted under a building's current zoning designation. Certain types of laboratory operations, particularly those involving higher biosafety levels such as BSL-2, BSL-3, and higher, may require special use permits, fire department approvals, and environmental review under local, state, or federal regulations. These labs handle potentially hazardous biological agents and are subject to stringent oversight to maintain compliance with public health, safety, and environmental standards. They must also meet specialized building code, ventilation, and containment requirements.
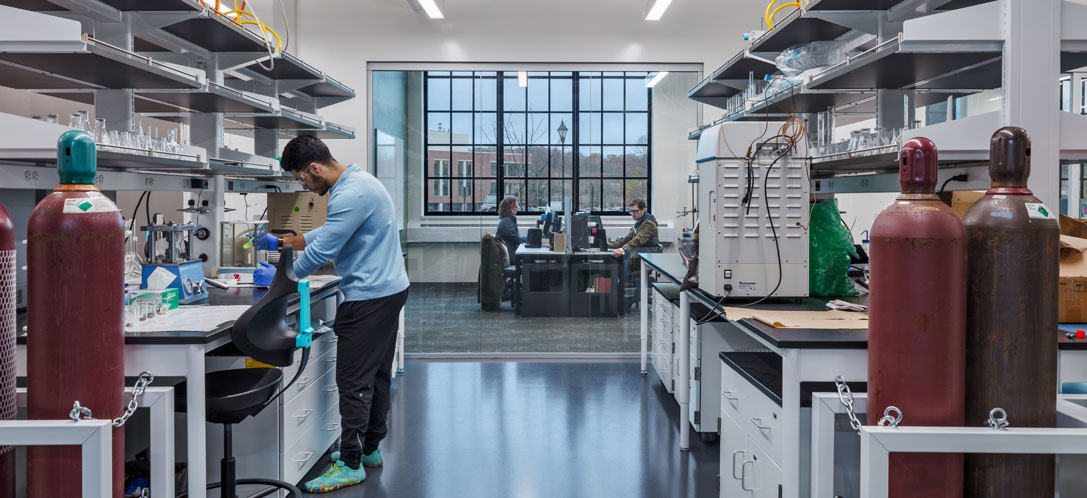
Natural light can enhance lab environments, but windows must be carefully evaluated for UV exposure to maintain controlled conditions.
Structural Upgrades: Floor Loads, Column Layouts, and Vibration
While office buildings are typically designed to accommodate people and light equipment, laboratories house a very different set of loads and functions.
- Floor loading: Heavy lab equipment, including biosafety cabinets, freezers, and imaging systems, may exceed the load-bearing capacity of office floors, requiring structural reinforcement.
- Bay spacing and column layout: Labs benefit from standardized, unobstructed layouts—typically with bays spaced between 10’-6” and 11’-0”. Column placement must support, not interrupt, lab aisles.
- Vibration control: Sensitive equipment requires strict vibration performance, often measured to NIST VC-A criteria. Vibration levels typically increase on higher floors, making upper levels in office buildings less suitable for sensitive equipment. While mitigation strategies like vibration isolation tables can reduce impact, early evaluation and planning are essential to ensure performance standards are met.
MEP Systems for High-Performance Research Labs
Mechanical, electrical, and plumbing systems in labs are far more intensive than those in office settings—and they often represent the largest cost category in a conversion project.
Electrical
Labs demand high-power loads due to specialized equipment, ventilation systems, and redundancies. It’s critical to:
- Evaluate and potentially upgrade electrical risers, transformers, and distribution panels.
- Account for lead times on electrical gear, which can impact construction schedules.
- Plan for standby power generation, utilizing either natural gas or diesel, which requires strategically planned, zoned, and screened locations for generators.
Mechanical
HVAC is a significant concern, not only in terms of capacity but also layout.
- Floor-to-floor heights: Labs often require 14 to 15 feet of vertical clearance to accommodate proper ductwork distribution. If this isn’t available, solutions include adding vertical shafts or horizontal distribution on screened roofs.
- HVAC upgrades: Upgrades should provide high exhaust rates, air changes, and strict temperature and humidity controls necessary for scientific accuracy and personnel safety.
- N+1 redundancy: Providing backup capacity for HVAC systems increases reliability, minimizes downtime, and allows maintenance or failure recovery without service interruption.
Plumbing
Plumbing requirements extend far beyond those of an office environment. Labs typically need:
- Emergency fixtures such as showers and eyewash stations.
- Specialized systems for gas and air lines.
- Chemical neutralization systems, particularly in chemistry or biopharma labs.
- Bulk gas storage, including a large nitrogen tank for modern lab applications.
Cost and Timeline: Office-to-Lab vs. Ground-Up Build
For owners weighing lab conversion against ground-up development, the potential for reduced capital expenditures and faster delivery timelines can make adaptive reuse an attractive strategy. In high-demand life science markets, these efficiencies can improve project ROI and create a competitive leasing advantage. However, these benefits are highly dependent on the existing building’s capacity to support lab-specific infrastructure as mentioned above. Architectural constraints, structural limitations, and outdated MEP systems can quickly erode anticipated savings and schedules—often surprising owners with unplanned complexity, cost, and delay.
Ultimately, transforming office buildings into laboratories hinges significantly on cost. This financial focus branches into several other considerations:
- Cost Per Square Foot: Analyze expenses across different space typologies, such as GxP-compliant versus non-GxP lab areas, and assess the financial implications of converting spaces to meet GxP standards. Cost variations between R&D and manufacturing spaces also warrant close scrutiny.
- Budget Alignment: Compare total construction costs against the overall project budget. This requires establishing realistic budgets through forecasting and continuous cost tracking during the project's progression.
- Capital Considerations: Evaluate the financial implications of leasing versus purchasing, including acquisition costs, financing options, and available tax incentives or abatements. Consider return-on-investment (ROI) models to support strategic decision-making.
- Cost Variability Factors: Account for regional differences in labor and material costs, proximity to supply chains and talent pools, and local permitting requirements. Identifying core cost drivers and major expenses helps manage finances efficiently, with value engineering and comprehensive cost analyses—above-the-line and below-the-line—offering tactical financial improvements.
Your Roadmap to a Successful Office-to-Lab Conversion
Repurposing speculative office buildings into R&D laboratories can be a powerful real estate strategy—if executed thoughtfully. Success hinges on early, detailed evaluations of a building’s infrastructure and regulatory context and close coordination between owners, architects, engineers, and contractors throughout design and construction.
To support informed decision-making, BHDP provides clients with:
- Conceptual hard cost data to shape early budget expectations.
- Insights into federal and state regulatory impacts on cost and design.
- Regional cost indexing tools to adjust for market conditions.
- Strategies for meeting sustainability and code compliance targets, such as ISO and ASHRAE standards.
- Performance-based design metrics like air changes per hour and vibration criteria to ensure lab-readiness.
With a proactive, multidisciplinary approach, these conversions can unlock real value, delivering high-performance labs that support the next generation of research and innovation.
Need help deciding between renovating or building new for your R&D lab? BHDP’s Discovery & Science team can assess your options and guide you toward the best-fit solution. Complete our contact form today to start the conversation.
Author
Content Type
Date
July 22, 2025
Market
Practice
Topic
Laboratory Design