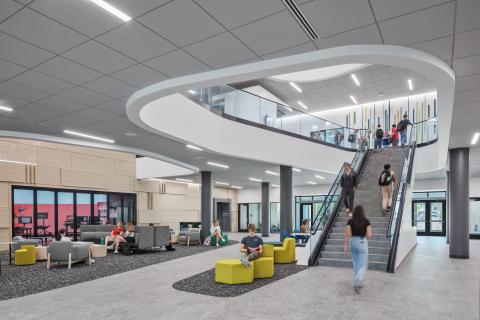
Capacity Planning in a Post-COVID Manufacturing World
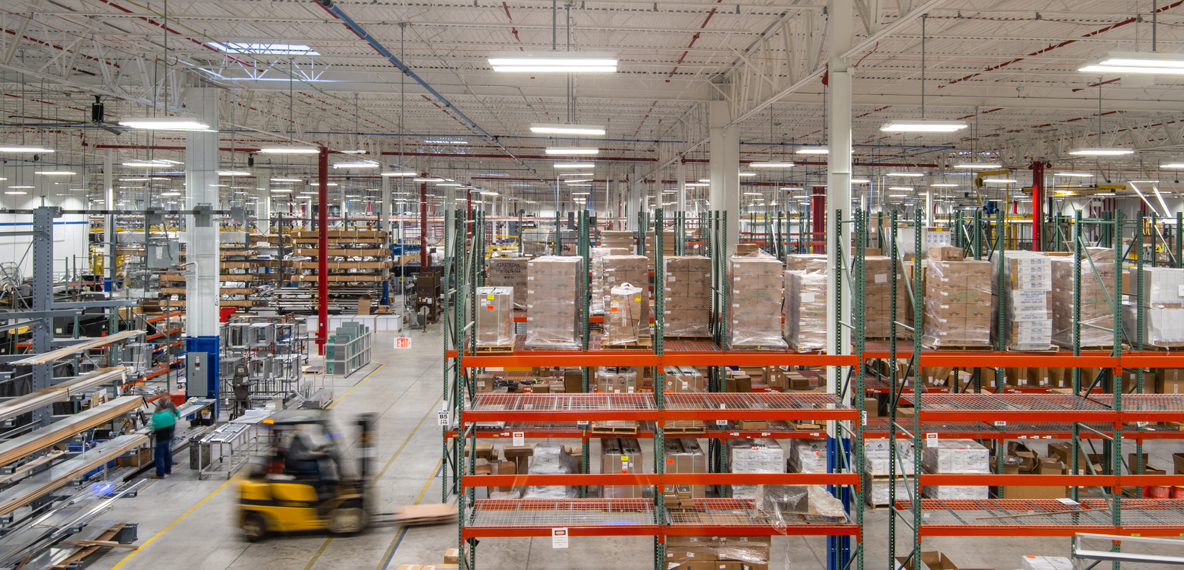
COVID-19 has had a notable impact on manufacturing in every industry sector. In a recent survey by the National Association of Manufacturers, almost 80% of manufacturers anticipated financial and operational consequences from the COVID-19 pandemic. Even prior to the pandemic, there was a notable shift from global to more local economies due in large part to international trade tensions, increased foreign wages, quality control and other factors; the pandemic only intensified this trend. Now, many industries are looking to bring supply chains (critical component/raw material production) closer to home, resulting in manufacturers building new production facilities or expanding existing facilities as a means of improving supply chain resiliency. This changing landscape is pushing companies to re-evaluate their processes and production capacities.
Forecast Production Volumes
Whether the industry is experiencing growth or anticipating a reduction in revenue, it is critically important to forecast the production volume demand accurately as this influences all aspects of the near and long-term growth strategy — from equipment asset utilization, to staffing and capital spending for new facilities and infrastructure.
There are multiple elements to consider. Compare 12-month rolling average sales with the previous three months to identify trends. Evaluate sales projections with actual revenues. Task sales or business development leaders with analyzing industry trends.
Consider the cost index of production and packaging materials and building materials with that of current interest rates. How will this influence customer’s near and long-term demand for products and services? Will inflation of material costs reduce consumer demand resulting in capacity demand reductions and idle assets, or are current near-zero interest rates an opportunity to invest in capital improvements, including expansions?
Don’t forget to consider the impact of government stimulus programs on the industry. For example, there are some bills in Congress meant to stimulate the airline industry, which may in turn significantly impact manufacturing suppliers that produce components to support the assembly and inspection of aircraft engines.
Maintain focus on the geopolitical and economic environment as well. Are there incentives to bring production back to the U.S.? Are there quality or supply chain reliability challenges companies are experiencing with offshore suppliers in developing countries? There are a multitude of interdependent factors to consider — every manufacturer is unique, necessitating the need to carefully evaluate each of these factors that may influence the production demand forecast and in turn the near- and long-term strategy for growth.
Calculate Throughput Levels
Understanding the throughput capabilities of production equipment factors into assessing your production volumes and capacity levels. When determining your equipment needs and planned capital spending, factor in equipment reliability, including downtime for change overs and scheduled maintenance because the equipment cannot always run at 100% capacity.
For example, consider a scenario where the demand forecast indicates a need to produce 1,000 units per hour. Even if a production line is rated at 1,000 units an hour, the actual throughput will need to be adjusted for downtime and reliability to gain a more accurate prediction of actual production capacity.
Once the actual throughput capacity per line is established, the next step is to translate that into the quantities and types of equipment needed to deliver the production demand, whether it is making systems, converting lines or packing systems. Remember to take into consideration that each production line, which will likely be multiple equipment modules, will typically have varying throughput capacities.
This will be critical when it comes to developing equipment general arrangements and beginning to plan for material delivery, maintenance and utility distribution to the lines. For example, on a single production line, someone may need two case erectors, but only one palletizer to avoid bottlenecks in the line.
Infrastructure Support
Understanding production volume and throughput capacity is only one part of the planning puzzle. One area that is easily overlooked is the infrastructure it takes to support the production operations: power, compressed air, domestic water, steam, as well as any waste byproduct that must be collected, treated and disposed of properly.
To add incremental capacity and additional equipment, what is required to support and bring that production line to life? Is there sufficient power, compressed air or steam? If not, is there a need to add an incremental transformer and switchgear, compressors or boilers to support the increased process utility demand. The addition of incremental utilities and their respective distribution will require proper space planning for the equipment as well as the distribution of pipes, cable tray, conduit, ductwork and so on to avoid creating interference or a barrier to future growth.
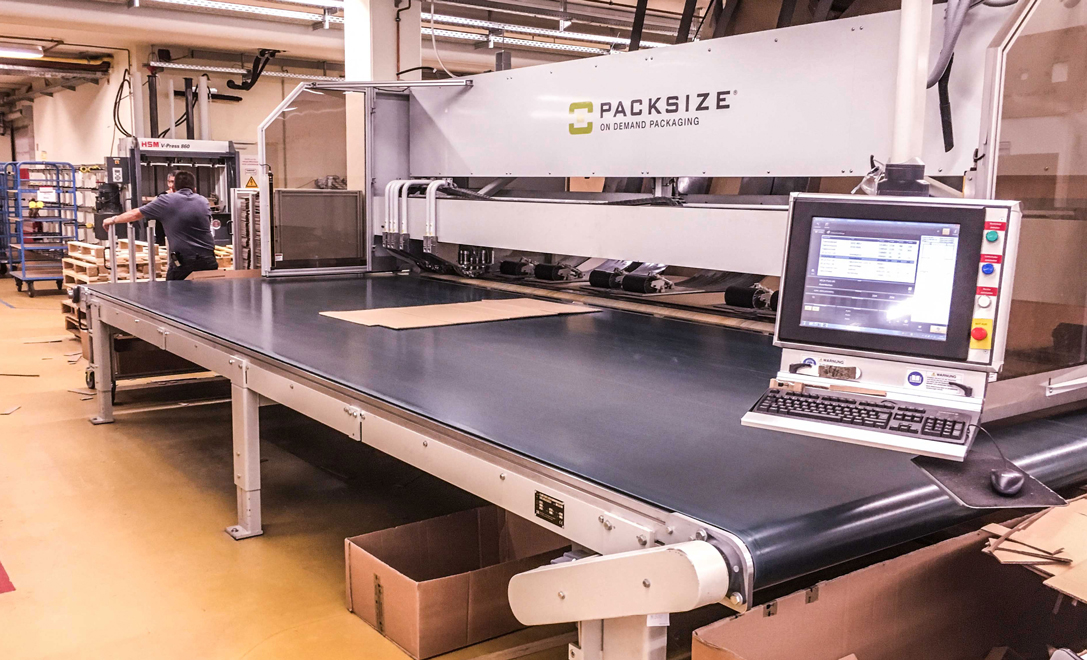
Custom shipping technology minimizes waste and excess storage of boxes.
In addition to utilities and utility distribution, investigate the upstream and downstream impact that an increase in production may have to other infrastructure areas. Increased production may require additional raw materials. Where will they be stored? Additional packing materials may also be required. Will additional or new types of racking systems be required? Will additional warehouse space be needed? Will more dock doors be required to receive materials or ship finished products? It is critical to conduct a comprehensive upstream and downstream study of your entire material storage strategy, utility requirements, onsite logistics and material flows, maintenance protocols, as well as staffing needs with each capacity increase initiative.
Consider a Sensitivity Analysis
Adding capacity to a manufacturing facility is not for the faint of heart. It is an expensive endeavor. Not only is the equipment a significant investment, but increasing capacity may also require additional staffing, raw materials and an investment in utility infrastructure. Consider conducting a sensitivity analysis, which is a front-end study that explores different scenarios to determine expansion thresholds and associated requirements.
For example, sales trends show that manufacturing company “ABC” needs to increase production capacity 15% to meet demand, and they commissioned a sensitivity study to analyze the existing production volume, as well as the spatial and utility impacts of adding additional production lines.
The sensitivity analysis showed that the company only had sufficient facility and utility capacity to add two incremental production lines. If they elect to add three new production lines, it will be a significantly higher investment because it would require additional transformers, more compressors and a building expansion. A sensitivity analysis presents owners with a best value options analysis (BVOA) of various capacity expansion scenarios to allow them to make informed decisions of how best to phase their long-term growth while managing their capital spending.
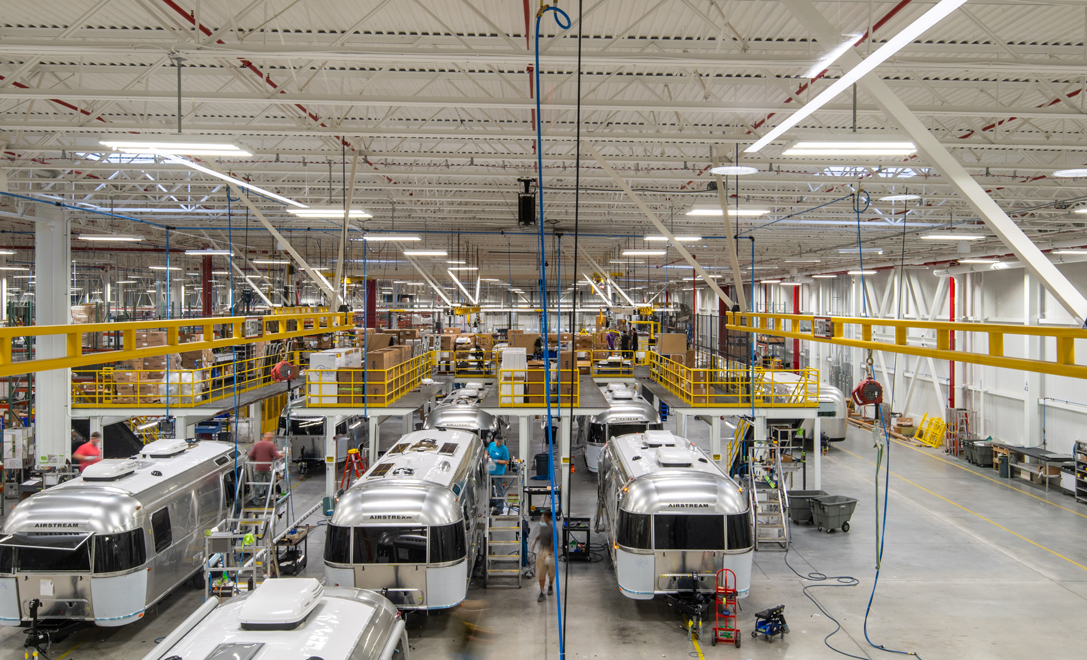
Mezzanine view of newly expanded capacity and opportunities for future increases.
Strategies for Future Capacity Expansion
In the example above, adding a third line would have been much more expensive. However, there are other costs such as construction mobilization/demobilization and plant downtime to take into consideration with each capacity initiative or building expansion decision.
If a building expansion is involved, consider expanding the production building to ultimately accommodate four new lines (four production bays) in the future but only install two new lines in an initial expansion phase.
This offers an opportunity to use the two empty bays for incremental raw material and packing material storage or warehousing of finished product in support of the two new lines on a temporary basis until such time that the third and fourth production lines are needed.
This approach also offers an opportunity to defer capital spending for new material storage space while protecting future production line installations. It also offers a benefit of minimizing disruptions to operations as a result of another production building expansion adjacent to operating lines.
This strategy provides the option of adding capacity incrementally as required with reduced downtime and the benefit of avoiding business interruptions due to a new capital expansion and construction project. The overall goal is to plan with a longer horizon in mind, which involves protecting the space that will ultimately be needed in the future without investing in the building or equipment now.
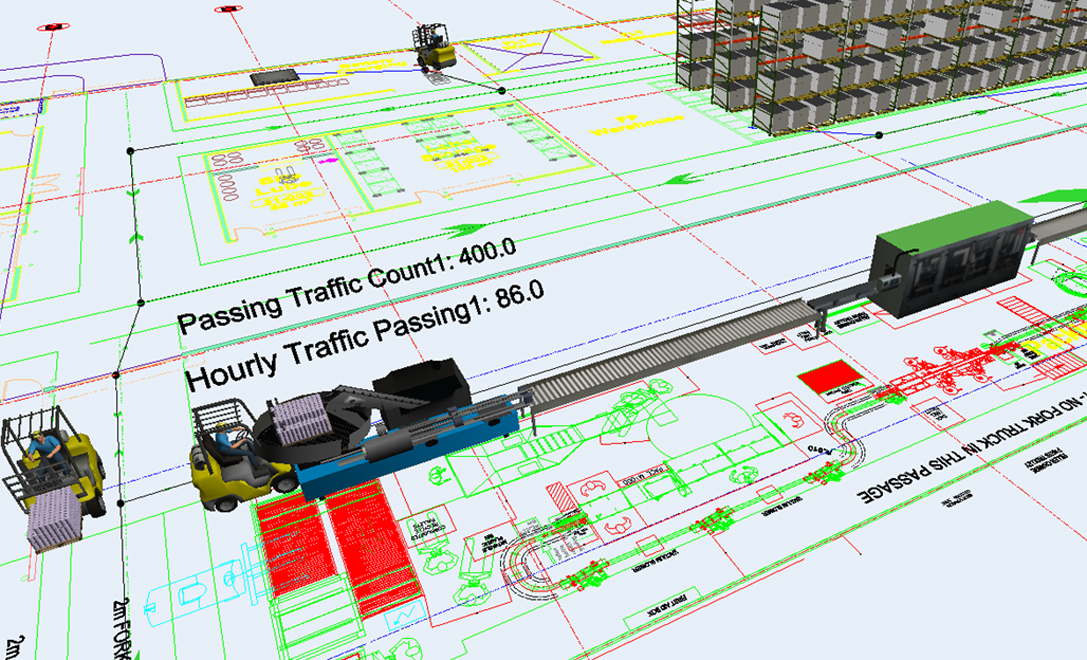
Data-informed designs from computer modeling that simulated increased production helped minimize bottlenecks.
Future capacity expansion requires advance planning and development of robust equipment general arrangements, location control plans and phasing strategies to ensure building expansions, equipment, material flows, utilities and utility distribution are synchronized.
That is why it is important to invest in a comprehensive site and facility master plan based on an aligned production capacity master plan. It is equally important to regularly review and update these plans as a business changes. Regular reviews and refinements to plans will ensure a focus on the long-term business objectives are maintained and that short-term decisions do not become barriers to long-term growth and success.
Capacity Planning is a Team Sport
As any successful sports coach will tell you, people need a team with the right experience to win a championship title. And, that applies to capacity planning, too. From the beginning, it is important to have a cross-section of expertise representing all aspects of the business at the planning table who are willing to share their unique insights. Early involvement of team members supports commitment to the capacity planning process. Ideally, the process is led by an individual who has a history with the company and experience working across multiple roles and functions throughout their career. By sharing the process with a cross-functional team, the capacity planning and expansion option development and evaluation process can be conducted in as little as eight to 12 weeks.
Increased Acceptance of Automation
Prior to the pandemic, many manufacturers were challenged to attract and retain skilled technicians to operate their production equipment. The pandemic required manufacturers to suspend operations or reduce the number of staff working to ensure worker safety, which led to backlogs in order fulfillment and severe supply chain shortages globally. As a result, manufacturing leaders are accelerating their investment in automation to improve supply chain resiliency in the future.
While the initial investment may be high, automation has multiple benefits. It can help protect workers’ health by minimizing contact with one another (automation requires fewer workers in a given space). It also has a benefit of increasing consistency in product quality, and over time can mitigate the impact of production cost due to rising wages whether production is offshore or domestic.
While manufacturers may not be able to invest in full-scale automation all at once, consider identifying one or two areas that could be automated and integrate into your overall capacity and master plans.
Capacity Planning Post-COVID-19
The manufacturing sector experienced significant disruption from COVID-19, but as organizations restart their operations, capacity planning combined with site and facility master planning can help leaders re-imagine a resilient and efficient future.
This article was originally published in Plant Engineering.
Author